The chemical industry has an integral function within the deployment of new energy technologies, specifically solar and wind. Depending at the specifics of the technologies, the material inputs vary, however it is no enhancement to say the chemical industry supports the renewable energy sector, in general, and solar, specially.
Steady upward push in global installed base
Photovoltaic (PV) cells – that convert incident solar energy into electricity that can be consumed right away, stored in batteries, or piped into electricity grids – have visible staggering growth in the last decade, and continue to do so. This has been pushed by way of technological developments which have increased their performance, as also big investments in production infrastructure – nicely beforehand of demands. The latter has had the expected outcome of decreasing costs, and even as this isn’t always accurate information for the PV cell or module manufacturers, user industries have substantially benefitted.
According to estimates through the International Energy Agency (IEA), a Paris-primarily based thinktank, global cumulative PV potential grew to 1.6-TW (Terawatts) [1-TW = 1,000 Gigawatts (GW)] in 2023, up from 1.2-TW in 2022, with 446-GW of capacity commissioned in the year. China, which has led solar energy deployment and incorporated module production at a scale unrivaled with the aid of any other country, on my own mounted 235-GW (~60% of global installations) – nearly equal to the full set up base in Europe, the world’s second largest marketplace, taking its accumulative established base to 665-GW.
India’s development in PV capacity has no longer been consistent in large part due to issues related to administrative strategies, grid entrance and financing. But in recent years, the development has been largely on an upward trajectory. In 2023, India had a slightly slower year (compared to the previous) with 16-GW of latest capability added, taking its installed base to close to 170-GW. This puts India at 4th place after (China, EU, USA) and simply in advance of Japan. A big bite (65%) of the installed PV base is in utility scale projects.
Tackling China’s dominance
PV markets have been extremely oversupplied for numerous years now, and stocks at manufacturers at the end of 2022 reached a quantity above that of the established in Europe and US combined. This situation descended further in 2023, and by the end of the year unsold stocks had been calculated at 150-GW, ensuing in big price drops alongside the value chain. According to S&P Global Commodity Insights (S&P), a consultancy, solar module prices drop 54% between 2022 and 2024 and will go down even more. Very quickly, prices may be a 1/1,000th the level in 1977 – significantly increasing affordability for consumers.
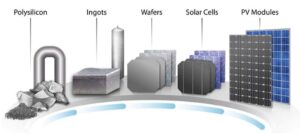
In 2023, China manufactured approximately 91% of the world’s polysilicon for solar PV modules, whilst India had zilch. As of 2024, China manufactured 97% of the world’s ingots and wafers, 80% of the cells, and 80% of the modules. The IEA calculated module production expenses in China are 10% less than in India, 20% less than in the US, and 35% less than in Europe. Large versions in energy, labour, funding and overhead costs provide an explanation for these variations,
For Indian manufacturers (and others outside of China) seeking to invest in combined PV cellular/module making this dominance has significantly challenged venture viability, and constrained production to simply panel assembly.
Policy and fiscal support
Governments – eager to build combined PV production to ramp up energy safety – have spoke back to industry pleas with monetary and policy guide. In India, a production Linked Incentive (PLI) Scheme is available for industry members and gives monetary incentives in the early years of operations, as also capital subsidies. The two stages of the PLI scheme had allocations of Rs. 4,500-crore and Rs. 19,500-crore, respectively, to permit 39.6-GW of producing capability across 11 enterprises.
Mandates also need government and government-supported ventures – which constitute about 70% of India’s module requirement – to source India-made modules. India also has imposed a 40% Basic Customs Duty (BCD) on imported solar modules and a 25% BCD on imported solar cells, but a loophole lets in them to go into tariff-free from nations with whom India has free trade agreements (e.g., Vietnam and Malaysia).
In the US, stiff anti-dumping and countervailing responsibilities had been imposed on imports even earlier than the ongoing tariff wars. Chinese enterprises who diversified their production bases to Southeast Asia to avoid the first lot of tariffs, may no longer advantage the given broad spread of country-specific tariffs that the US has simply imposed. How these tariffs will evolve in time is, but, anybody’s wager at this point.
S&P reckons that the incentives and the tariffs on imports from China have largely bridged the gap in module producing costs between India and China. India’s measures (and of other nations), it reckons may want to lower China’s market share of PV module capacity from 78% now to 68% by 2029.
In the upstream supply chain like polysilicon, ingots, and wafers, India has decrease funding costs than Europe and the USA (although no longer China) and could emerge an options provider to China. These inputs are more capital-, energy-, and technology-in depth than solar cells and modules, ensuing in extra capital expenditures, working charges, and technical complexities. numerous, Indian enterprises – Indosol Solar, Reliance New Energy Solar, Adani Infrastructure, and FS India Solar Ventures – plans to construct combined facilities, which embody production from polysilicon to modules, and are relying on an allowing policy framework to stay competitive.
Technology shifts
While crystalline silicon remains the essential technology for PV cells (and likely to stay that manner for a while), technology growth have led to a consistent development in efficiencies (the fraction of incident solar energy transformed to beneficial electricity). At the turn of this century, efficiencies of the first-class ‘p-kind’ cells had been inside the range of 15-19%, which nudged up to 18-23% in the Passivated Emitter and Rear Contact (PERC) solar cells, which have an additional reflective layer on the back. The present day lot of ‘n-type’ cells supply efficiencies of 22-25%, at the same time as hybrid thin-film structures underneath growth can move up to 25-30%. Perovskites, touted as an opportunity to silicon, are stated to offer efficiency ranges upward of 25%, though their toughness stays a trouble. Their different benefits consist of less complicated processing and manufacturing, and decrease weight (by using an order of magnitude).
While lots of the mounted PV base globally just 4 years in the past had been first generation ‘p-type’ monofacials, the ‘n-sorts’ have accrued marketplace share and now account for 90% as they’re the choice for new installations. Thin-film technologies still constitute a small niche, and probably to stay that way at the least till the end of the decade.
A lot of the development in the industry is at the module level – in preference to the cell – and bifacial systems, which generate electricity from each front and back panels, are now the preferred system despite their greater tough set up and higher charges. Their share of the mounted base is anticipated to attain 60% by 2029.
Material choices changing
Solar panels want a variety of materials apart of the core PV cell. These include the front sheet of glass to obtain sunlight; encapsulants that bond the cell and sheets and commonly made of ethylene vinyl acetate (EVA) copolymer or polyolefin elastomer (POE); and back-sheet, fabricated from one or greater polymers.
The back-sheet is a complicated sandwich structure comprising a polyester (PET) thick film, that acts as a core and offers electrical insulation; and a polyvinyl fluoride (PVF) or polyvinylidene fluoride (PVDF) layer that acts as the outer and internal layer, defensive against moisture ingress and environmental conditions.
The migration to ‘n-kind’ bifacial systems will change the forms of polymers used. While EVA dominates the encapsulant marketplace for monofacial ‘p-kind’ PV cells, POE is showing quicker increase in keeping with ‘n-type’ and bifacial markets. S&P estimates that the share of POE among encapsulants will double by 2030 from modern levels, at the rate of EVA.
Recycling – for sustainability and supply protection
Recycling of solar PV panels gives environmental, social and economic advantages while improving safety of supply in the long time. The IEA estimates that if panels have been systematically gathered at the end of their lifetime, supplies from recycling them should meet over 20% of the solar PV industry’s require for aluminium, copper, glass, silicon and almost 70% for silver between 2040 and 2050. However, present PV recycling strategies struggle to generate enough sales from the recovered material to cover the cost of the recycling process.
India’s private quarter is driving a concerted bid to end up an integrated base for PV. With the right method and an permitting policy environment enterprises can goal no longer simply to deal with the domestic marketplace, however also global ones.